Managing Environmentally Friendly Palm Oil Mills
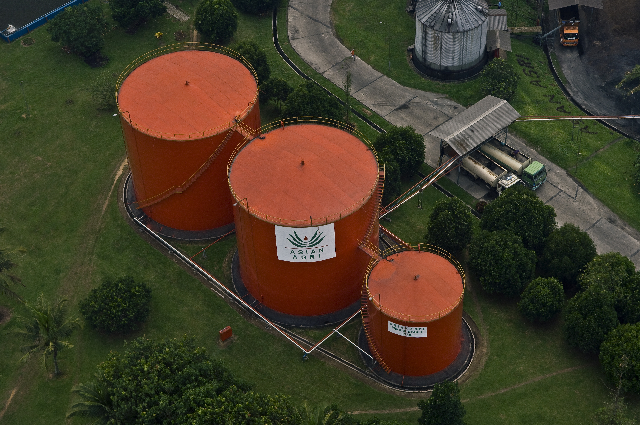
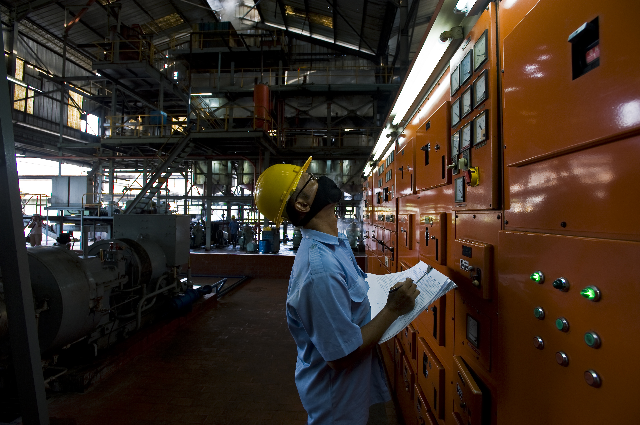
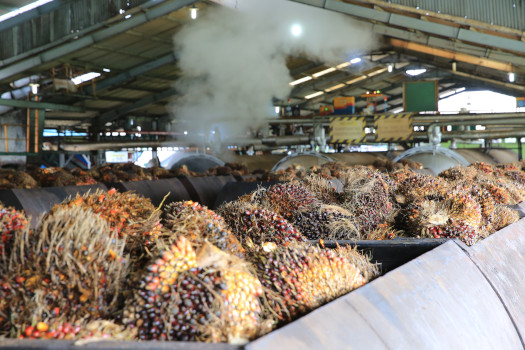
Asian Agri manages 22 mills to produce more than 1.1 million metric tons of palm oil is extracted CPO (Crude Palm Oil). The extraction process begins with the transportation of ripe Fresh Fruit Bunches (FFB) harvested from plantations to the mills. FFBs are then sterilized using steam for half an hour, which also serves to remove the fruits from the bunch. The fruits are then moved to a pressing station, which then goes through a clarification process to remove moisture, residue and dirt. The end product is CPO.
Asian Agri operates ten units of biogas power plants that convert the methane gas to electricity. The power plants located in North Sumatra, Riau and Jambi produce renewable energy from Palm Oil Methane Effluent (POME) for its mills and to support electricity supply to rural areas.
In line with Asian Agri’s commitment to support the preservation of nature and resources, one of the concrete steps is to reduce the use of water for mills operational need. We always conduct a regular maintenance on pipes, pumps and machines, so that the mills always operate in optimal conditions, and if a potential leak is seen, we can immediately overcome it to prevent waste in the use of water. The intensity of water use in Asian Agri from 2018 has decreased significantly, from 6.21 m3 per tons of CPO to 6.01 m3 per tons of CPO in 2019 and 5.66 m3 per tons of CPO produced in 2020.
Closed-Loop Process
Asian Agri operates a closed-loop process to ensure maximum efficiency. Empty bunches are returned to the plantations for use as organic fertilizer, while the byproducts such as mesocarp fiber as used as bio-energy to replace fossil fuels.
Palm kernels are dried, broken and separated to produce palm kernels, which are sold as a final product or further processed to obtain crude palm kernel oil.
All mill waste is discharged into a system of sewage treatment ponds where anaerobic and aerobic processes take over to produce fertilizer, protecting waterways from pollution.